Библиотека
Теология
Конфессии
Иностранные языки
Другие проекты
|
Комментарии (3)
Карпенков С. Концепции современного естествознания: Учебник для вузов
ЭВОЛЮЦИЯ ЕСТЕСТВЕННО-НАУЧНЫХ ЗНАНИЙ О ВЕЩЕСТВЕ
6.8. Новые химические элементы и изотопы
Продолжение периодической системы элементов
Многогранная деятельность людей осуществляется в материальной сфере, заполненной многочисленными соединениями и их составляющими – элементами периодической системы Менделеева. Еще до 30-х годов нашего столетия эта система состояла из 88 элементов. С учетом свободных клеток с номерами: 43 (технеций), 61 (прометий), 85 (астат) и 87 (франций), в ней было всего 92 места. Элемент с атомным номером 92 – это уран.
Предполагается, что на первоначальной стадии развития Земли существовали и трансурановые элементы с порядковыми номерами до 106. Такие элементы имели небольшую продолжительность жизни по сравнению с возрастом Земли и поэтому полностью распались. Самым долгоживущим элементом и данной группы оказался плутоний-244 с периодом полураспада 82,2 млн. лет, и его существование на Земле поэтому вполне вероятно. И действительно в 1971 г. из калифорнийского минерала бастнезитс удалось выделить от 10 до 20 млн. атомов плутония Рu244, которые были надежно идентифицированы с по мощью массспектроскопии. Так уран перестал был самым последним в системе Менделеева и самым тяжелым из всех существующих в природе элементов.
В 1940 г. был получен первый трансурановый элемент – нептуний, а за три года до этого открыт первый искусственный элемент – технеций. Затем в лабораторных условиях были зарегистрированы еще 15 трансурановых элементов с атомными номерами до 107. В Объединенном институте ядерных исследований в подмосковном городе Дубна были открыты элементы с номерами 104 (1964г.), 105 (1970г.), 106 (1974 г.) и 107 (1976 г.). Элемент с номером 104 носит название курчатовий в честь академика И. В. Курчатова (1902/03–1960) – выдающегося физика, организатора и руководителя работ по атомной науке и технике в СССР.
Международный союз чистой и прикладной химии в сентябре 1997 г. узаконил названия искусственных сверхтяжелых элементов: резерфордий, дубний, сиборгий, борий, хассий и мейтнерий. Эти названия даны главным образом в честь ученых, внесших большой вклад в ядерную физику. Один из данных элементов – дубний – назван в честь города Дубны, где были открыты многие новые химические элементы.
В феврале 1999 г. появилось сообщение о том, что ученые из Объединенного института ядерных исследований в Дубне открыли выходящий за пределы периодической таблицы Менделеева новый химический элемент с периодом полураспада намного большим, чем для открытых в последнее время сверхтяжелых элементов.
Трансурановые элементы с атомными номерами до 100 можно получить в ядерном реакторе путем «надстройки» ядер изотопа урана-238 бомбардирующими нейтронами. Все элементы с номерами более 100 и массовыми числами более 257 получают только в ускорителях и в незначительных количествах.
Для получения сверхтяжелых трансуранидов производится бомбардировка урана ионами ксенона, гадолиния, самария, гафния или урана. Особенно эффективна бомбардировка ионами самого урана, в результате которой образуются чрезвычайно тяжелые промежуточные ядра. Изучение таких реакций стало возможным только с 1971 г., когда мощность ускорителей позволила ускорить тяжелые ионы до достаточно высоких энергий.
В стабильных атомных ядрах заряженные и нейтральные частицы находятся в равновесном состоянии. С нарушением равновесия ядерная система становится неустойчивой. Современная теория позволяет рассчитать с вполне определенной вероятностью стабильность сверхтяжелых ионов и элементов, а также предсказать наиболее вероятные их физические и химические свойства. Из подобных расчетов вытекает, что элементы с атомными номерами между 114 и 164 должны обладать неожиданно высокой стабильностью (см. рис 6.9). Такие элементы образуют своеобразный остров стабильности, на котором возможно существование изотопов с периодом полураспада до 108 лет.
Предполагается, что свойства элементов с атомными номерами 112–118 аналогичны свойствам элементов в ряду ртуть–радон. Верхняя граница возможной стабильности, насколько ее позволяет определить современный уровень естественно-научных знаний, приближается к атомному номеру 174. Для синтеза подобного рода элементов нужны новые экспериментальные методы и новые технические средства эксперимента.
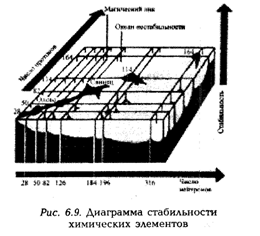
Радиоактивные изотопы
Изотопы – разновидности химических элементов, у которых ядра атомов отличаются числом нейтронов, но содержат одинаковое число протонов и поэтому занимают одно и то же место в периодической системе элементов. Различают устойчивые (стабильные) и радиоактивные изотопы. Термин «изотопы» впервые предложил в 1910г. Фредерик Содди (1877–1956), известный английский радиохимик, лауреат Нобелевской премии 1921 г., экспериментально доказавший образование радия из урана.
Радиоактивные изотопы широко применяются не только в атомной энергетике, но и в разнообразной приборной технике, медицине и т. п. В промышленно развитых странах выпускается множество приборов и аппаратов, содержащих радиоактивные изотопы. Все они служат для определения плотности, однородности, гигроскопичности и других характеристик разных материалов.
С помощью радиоактивных изотопов можно проследить за перемещением химических соединений при физических, технологических, биологических или химических процессах. Для этого используются меченые атомы (радиоактивные индикаторы). Исследуемое вещество вводят радиоактивные изотопы определенных элементов, тем самым метят его, и затем наблюдают за движением меченых атомов. Данный способ позволяет исследовать механизмы реакций при превращениях веществ в сложных условиях, например, в доменной печи или в аммиачном реакторе, а также изучать процессы обмена веществ в живых организмах. Например, введение изотопа азота-15 позволяет исследовать процесс биологического связывания азота воздуха растениями семейства бобовых (гороха, клевера, вики и др.). Изотоп кислорода-18 помогает выяснить механизм дыхания живых организмов.
Радиоактивный метод анализа вещества дает возможность определить содержание в нем различных металлов от кальция до цинка, в чрезвычайно малых концентрациях – до 10-10 (для этого требуется всего лишь 10-12 г вещества).
Радиоактивные препараты оказались полезными и в медицинской практике. С их помощью осуществляется лечение многих заболеваний, в том числе и злокачественных опухолей.
Изотопы плутония-238, кюрия-224 и др. могут применяться для производства батарей небольшой мощности – от киловатта до милливатта. Они могут использоваться, например, в приборах для стабилизации ритма сердца. При этом для бесперебойной работы на протяжении по крайней мере 10 лет достаточно всего 150–200 мг плутония (оксидортутные батареи служат до 4 лет).
В результате радиационно-химических реакций из кислорода образуется озон, из газообразных парафинов – водород и сложные соединения низкомолекулярных олефинов. Облучение полиэтилена, поливинилхлорида и многих других полимеров приводит к повышению их термостойкости и прочности. Можно привести множество других примеров практического применения изотопов и радиоактивного излучения. Несмотря на это отношение людей к радиации, особенно в последние десятилетия, резко изменилось. За примерно столетнюю историю радиоактивные источники прошли долгий путь от эликсира жизни до символа зла.
От радиоактивной эйфории до радиофобии
После открытия рентгеновских лучей многие люди верили, что с помощью радиации можно вылечить все болезни и решить все проблемы. В то время люди не хотели видеть опасности радиоактивного облучения.
Когда в 1895 году Вильгельм Конрад Рентген обнаружил новый вид облучения, волна восторга охватила весь цивилизованный мир. Открытие не только поколебало основы классической физики. Оно обещало неограниченные возможности – в медицине его тут же стали применять для диагностики, чуть позже – для лечения самых различных заболеваний. Рентгенодиагностика и рентгенотерапия спасли жизнь многим людям. Врачи, правда, через некоторое время стал ограничивать допустимое число рентгеновских снимков для одного пациента, но никто всерьез не обращал внимания на ожоги, возникающие после рентгена. Французский физик А. Беккерель, например, имел привычку носить в кармане брюк радиевый прибор. Через некоторое время он заметил воспаление на ноге. Чтобы убедиться, что прибор послужил причиной болезни, он переложил его в другой карман. Но даже появившаяся на другой ноге язва не смогла отрезвить ученого, находящегося, как и остальные, в эйфории нового открытия. Радиоактивное излучение в то время рассматривали как универсальное целительное средство, эликсир жизни. Радий оказался эффективен при лечении доброкачественных опухолей, и «популярность» его резко возросла. В свободной продаже появились радиевые подушки, радиоактивная зубная паста и косметика.
Однако вскоре появились первые тревожные сигналы. Уже в 1911 г. было обнаружено, что берлинские медики, имеющие дело с радиацией, часто заболевают лейкемией. Позднее Макс фон Лауэ экспериментально доказал, что радиоактивное излучение неблагоприятно влияет на живые организмы, а в 1925–27 гг. стало известно, что под воздействием излучения возникают изменения наследственного вещества – мутации.
Между тем полное отрезвление наступило, вероятно, после атомной бомбардировки Хиросимы и Нагасаки. Почти все оставшиеся в живых после ядерного взрыва, получили большую дозу облучения и умерли от рака, а их дети унаследовали некоторые генетические нарушения, вызванные радиацией. Впервые об этом стали открыто говорить в 1950г., когда число больных лейкемией среди пострадавших от атомных взрывов стало катастрофически расти. После Чернобыльской аварии недоверие к радиации переросло в настоящую ядерную истерию.
Таким образом, если в начале XX в. люди упорно не хотели видеть вреда от облучения, то в конце его стали боятся радиации даже тогда, когда она не представляет собой реальной опасности. Причина обоих явлений одна – человеческое невежество. Можно только надеяться, что в следующем веке человечество научится придерживаться золотой середины и обращать знания о природных явлениях себе во благо.
Плазмохимические процессы
Плазмохимические процессы протекают в слабоионизированной, или низкотемпературной плазме, при температуре от 1000 до 10 000° С. Такие процессы характеризуются возбужденным состоянием ионизированных и неионизированных частиц, столкновения которых приводят к очень высокой скорости химических реакций.
В плазмохимических процессах скорость перераспределения химических связей между реагирующими частицами очень высока: длительность элементарных актов химических превращений составляет около 10-13 с при почти полном отсутствии обратимости реакции. Такая скорость в обычных заводских реакторах из-за обратимости снижается в тысячи и миллионы раз, поэтому плазмохимические процессы высокопроизводительны.
Производительность метанового плазмохимического реактора – плазмотрона крохотных размеров (длиной 65см и диаметром 15см) – составляет 75т ацетилена в сутки. По производительности такой плазмотрон не уступает огромному заводу. В реакторе при температуре 3000–3500° С за одну десятитысячную долю секунды около 80% метана превращается в ацетилен. Степень использования энергии достигает 90– 95%, а энергозатраты составляют не более 3 кВт.ч на 1 кг ацетилена. В то же время в паровом реакторе пиролиза метана энергозатраты вдвое больше.
В последнее время разработан эффективный способ связывания атмосферного азота посредством плазмохимического синтеза оксида азота, который гораздо экономичнее традиционного аммиачного способа. Создана плазмохимическая технология производства мелкодисперсных порошков – основного сырья для бурно развивающейся порошковой металлургии. Разработаны плазмохимические методы синтеза карбидов, нитридов, карбонитридов таких металлов, как титан, цирконий, ванадий, ниобий и молибден, при сравнительно небольших энергозатратах – 1–2 кВт. ч на 1кг готовой продукции. Плазмохимические способы промышленного производства многих видов химической продукции отличаются высокой производительностью при сравнительно небольших затратах энергии.
В 70-х годах XX в. созданы плазмохимические сталеплавильные печи, производящие высококачественный металл. Именно таким печам принадлежит будущее электрометаллургии. В результате ионно-плазменной обработки можно сформировать, например, пористый рельеф на ровной поверхности (см. рис. 6.10). Ионно-плазменная обработка рабочей поверхности инструментов позволяет увеличить их износостойкость в несколько раз. В результате подобной обработки можно сформировать, например, пористый рельеф на ровной поверхности (см. рис. 6.10). Ионно-плазменное напыление в вакууме широко применяется для формирования элементов микронных размеров современных интегральных схем микроэлектроники.
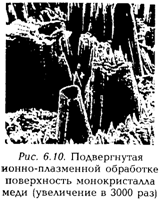
Методом плазменного напыления можно нанести пористое покрытие со сложной микроструктурой, которая способствует срастанию эндопротеза с костной тканью. Такие покрытия обладают большой удельной поверхностью. С их помощью можно увеличить эффективность катализатора для дожигания выхлопных газов автомобиля. Пористые покрытия, нанесенные на поверхность теплообменников, увеличивают коэффициент теплоотдачи, а пористые керамические покрытия служат надежной защитой от теплопотерь.
Плазмохимия позволяет синтезировать такие ранее неизвестные материалы, как металлобетон, в котором в качестве связующих материалов используются сталь, чугун, алюминий. Металлобетон образуется при сплавлении частиц горной породы с металлом и по прочности превосходит обычный бетон: на сжатие в 10 раз и на растяжение в 100 раз.
В нашей стране разработан плазмохимический способ превращения угля в жидкое топливо без применения высоких давлений и выброса золы и серы. Кроме основного химического продукта – синтез-газа, извлекаемого из органических соединений каменного или бурого угля, данный способ позволяет получить из его неорганических включений ценные соединения: технический кремний, карбосолилиций, ферросилиций, адсорбенты для очистки воды и т. п., – которые при других способах переработки угля выбрасываются в виде зольных отходов.
Таким образом, плазмохимические технологии, внедрившись в химическую промышленность сравнительно недавно, охватывают все больший круг различных отраслей современной промышленности.
Самораспространяющийся высокотемпературный синтез
Для производства многих тугоплавких и керамических материалов применяется технология порошковой металлургии, включающая операции прессования при высоком давлении и спекании полученной заготовки при относительно высокой температуре – 1200– 2000о С. Однако данная технология довольно энергоемкая: создание высоких температур и давления требует больших энергозатрат. Гораздо проще и экономичнее предложенная сравнительно недавно технология самораспространяющегося высокотемпературного синтеза, основанная на реакции горения одного металла в другом или металла в азоте, углероде, кремнии и т. п.
Процесс горения чаще всего представляется в виде взаимодействия кислорода с горючим веществом: углем, нефтепродуктами, древесиной и др. Обычно принято считать горение реакцией окисления горючего вещества, что с точки зрения окислительно-восстановительного процесса означает перераспределение электронов между атомами восстановителя–горючего тела и окислителя–кислорода. В таком смысле процесс горения возможен не только в кислороде, но и в других окислителях.
Самораспространяющийся высокотемпературный синтез – тепловой процесс горения в твердых телах. Он представляет собой, например, горение порошка титана в порошке бора или порошка циркония в порошке кремния.
В результате самораспространяющегося высокотемпературного синтеза получено множество тугоплавких соединений высокого качества:
· карбиды металлов: TiC, ZrC, HfC, VC, NbC,
Ta2C, TaC;
· бориды: TiB, TiB2, HfB2,VB, V3B2, NiB;
· силициды: TiSi3, ZrSi, ZrSi2, MoSi2;
· алюминиды: NiAl, CoAl;
· селениды: NbSe2, MoSe2, TaSe2, WSe2,.
Технология самораспространяющегося высокотемпературного синтеза не требует громоздких процессов и печей и отличается высокой технологичностью. Данная технология легко поддается автоматизации. Промышленной установкой, производящей многотоннажную продукцию, может управлять всего лишь один оператор.
Химические реакции при высоких давлениях
Химические превращения веществ при давлениях выше 100 атм относятся к химии высоких давлений, а при давлениях выше 1000 атм – к химии сверхвысоких давлений. Идея активизации химических реакций при высоком давлении возникла сравнительно давно: еще с 1917г. аммиачное производство осуществлялось при давлении 300 атм и температуре 600° С. В последние десятилетия с развитием космической технологии и синтезом искусственного алмаза произошли существенные изменения в химии высоких и сверхвысоких давлений. Во многих опытно-промышленных установках достигается 5000 атм. Уже проводятся испытания при давлении выше 600 000 атм, которое возникает за счет ударной волны при взрыве в течение миллионной доли секунды. Ядерные взрывы сопровождаются еще более высоким давлением.
При высоком давлении сближаются и деформируются электронные оболочки атомов, вследствие чего повышается химическая реакционная способность реагентов. При давлении 102–103 атм исчезает различие между жидкой и газовой, а при 103–105 атм– между твердой и жидкой фазами. При повышении давления до 106 атм образуется металлическая связь. Более высокое давление приводит к образованию неупорядоченного конгломерата электронов и ядер, подобного плазме.
Высокое давление ведет к существенному изменению физических и химических свойств вещества. Например, сталь при давлении 12 000 атм становится ковкой и гибкой, а при 20 000 атм металл эластичен, как каучук. При давлении 400 000 атм элементная сера – диэлектрик при обычном давлении – приобретает электропроводящие свойства. Обычная вода при высоких температурах и давлениях становится химически активной, и растворимость солей в ней становится в 3–4 раза выше, чем при нормальных условиях.
С повышением давления многие вещества переходят в металлическое состояние. Таким необычным свойством обладает даже газообразный водород – его металлическое состояние наблюдалось в 1973 г. при давлении 2,8 млн. атм. Металлический водород уже при 100 К переходит в сверхпроводящее состояние. С применением твердого водорода в качестве ракетного топлива полезный груз ракеты увеличивается с 10 до 60%.
Синтез алмазов
Одно из важнейших достижений химии сверхвысоких давлений – синтез алмазов. Искусственные алмазы были синтезированы в 1954 г. (после длительной, пятидесятилетней поисковой работы) почти одновременно в США и Швеции. Синтез осуществлялся при давлении 50 000 атм и температуре 2000°С. Первые искусственные алмазы стоили в 30 раз дороже природных, но уже к началу 60-х годов их стоимость существенно снизилась. В последние десятилетия ежегодно производятся тонны синтетических алмазов, по своим свойствам незначительно отличающихся от природных. Различия между синтетическими и природными алмазами можно определить только с помощью точных физических приборов. Доля искусственных алмазов на мировом рынке превышает 75%, от объема всей алмазной продукции.
В недалеком прошлом по производству и потреблению алмазов первое место в мире занимал бывший СССР. Более 8000 предприятий в нашей стране пользовались алмазным инструментом, причем советская промышленность производила более 2500 видов таких инструментов – от крошечных волочильных устройств до громадных режущих дисков для крупных каменных блоков.
Промышленный синтез алмазов основан на превращении графита в реакторе высокого давления (рис. 6.11). Катализатором при таком превращении служат различные вещества: металлический никель, сложные смеси железа, никеля и хрома, смеси карбида железа Fe3C с графитом. Кристаллизация алмазов происходит при давлении 50 000–60 000 атм и температуре 1400–1600° С. Алмазы можно синтезировать и с применением ударных волн.
Обычно в реакторах высокого давления синтезируются алмазные кристаллы размером не более 1 мм. Такие мелкие камни вполне пригодны для промышленных целей, но из них трудно изготовить украшения. Сравнительно недавно разработана новая технология, позволяющая выращивать кристаллы алмаза размером до 6мм. По такой технологии небольшие кристаллы алмаза вначале растворяют в расплавленном катализаторе и затем в более холодные области расплава помещают в качестве затравки крошечные алмазинки. Процесс кристаллизации алмазов при этом длится несколько суток при давлении 55 000–60 000 атм и температуре 1400–1500° С. Данная технология позволяет выращивать монокристаллы алмаза относительно крупных размеров и высокого качества. Синтез алмазов, которые можно было бы превратить в крупные бриллианты так сложен и дорог, что синтезированные бриллианты не могут конкурировать с природными: кристалл искусственного алмаза массой 50–60 г (250– 300 карат) стоит столько же, сколько 1 т золота.
Искусственные алмазы применяют преимущественно для промышленных целей. Алмазные порошки и пасты, режущее и буровое оборудование с алмазными кристаллами оказались незаменимыми во многих отраслях промышленности. Алмазная технология позволяет повысить производительность труда на 30–50, а в некоторых случаях и на 100%. Искусственные алмазы находят применение при изготовлении часов, прецизионных приборов. Ими режут и обрабатывают твердые металлы, керамику, стекло и т. д. С их помощью изготовляют тончайшую проволоку.
Синтезирована особая разновидность черных алмазов, называемая карбонадо, которая тверже алмазов, встречающихся в природе. Карбонадо синтезирован методом порошковой металлургии – путем спекания обычного алмазного порошка при давлении 30–80 тыс. атм и температуре 1000° С. Карбонадо позволяет обрабатывать сами алмазы, из него изготавливаются сверхтвердые буровые коронки.
По своей структуре алмаз отличается от графита более плотной упаковкой атомов углерода в кристалле (рис. 6.11). В 1985 г. была синтезирована новая разновидность многоатомных молекул углерода в виде шаров и состоящая из очень большого числа (от 32 до 90) атомов углерода. Самой устойчивой оказалась молекула С60, названная фуллероном (рис.6.12). За открытие новой формы многоатомных молекул углерода – фуллеронов – английскому ученому Гарольду Крото и двум его американским коллегам – Роберту Керлу и Ричарду Смелли присуждена Нобелевская премия по химии в 1996 г. К этому открытию привели многолетние работы по расшифровке спектральных линий поглощения межзвездного вещества. Было ясно, что они связаны с углеродом, но в какой форме объединяются атомы углерода – долго оставалось загадкой. И только в результате моделирования в лабораторных условиях так называемой углеродной звезды удалось синтезировать молекулы углерода в виде шаров.
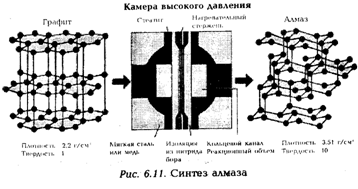
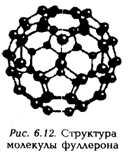
Фуллероны имеют исключительно высокую удельную емкость по водороду. В результате реакции присоединения водорода по ненасыщенным двойным связям углерода при высоких давлениях и температуре можно осуществить модификацию фуллеронов, что представляет практический интерес при создании перспективных аккумуляторов водорода.
Дальнейшие работы привели к созданию не только сферических молекул, но и эллипсоидальных (барелленов), трубчатых (тубеленов) и молекул других конфигураций. Из таких молекул можно создавать материалы невиданной прочности, элементы компьютеров XXI в., получать сита, способные разделять отдельные атомы по размерам.
Несмотря на рост производства искусственных алмазов и их широкое применение, обычные твердые материалы в виде различных карбидов металлов не утратили своей практической значимости. Хотя карбиды металлов менее тверды, чем алмазы, зато они более термостойки.
Сравнительно недавно из нитрида бора синтезирован материал, который тверже алмаза. При давлении 100 000 атм и температуре 2000° С нитрид бора превращается в боразон – материал, пригодный для сверления и шлифования деталей из чрезвычайно твердых материалов при очень высоких температурах.
К настоящему времени налажено промышленное производство не только искусственных алмазов, но и других драгоценных камней: корунда (красного рубина и синего сапфира), изумруда и др.
6.10. Синтетические материалы
Общие сведения
Материалы – это вещества из которых изготавливается различная продукция: изделия и устройства, машины и самолеты, мосты и здания, космические аппараты и микроэлектронные схемы, ускорители заряженных частиц и атомные реакторы, одежда, обувь и многое другое. Для каждого вида продукции нужны свои материалы с вполне определенными характеристиками. К свойствам материалов всегда предъявлялись и предъявляются высокие требования. Хотя современные технологии и позволяют производить множество разнообразных высококачественных материалов, однако проблема создания новых материалов с лучшими свойствами остается актуальной и по сей день.
При поиске нового материала с заданными свойствами важно установить его состав и структуру, а также обеспечить условия для управления ими. Результат поиска во многом зависит от чувствительности и разрешающей способности приборов, с помощью которых определяются состав и структура синтезируемого материала. Такие приборы создаются на основе только самых последних достижений естествознания и прежде всего физики. При обработке материала и изготовлении окончательной продукции, необходимой для потребления, не менее важны инженерно-технические достижения, позволяющие производить продукцию высокого качества.
В последние десятилетия синтезированы материалы, обладающие удивительными свойствами, например, материалы тепловых экранов для космических аппаратов, высокотемпературные сверхпроводники и т. п. Вряд ли можно перечислить все виды современных материалов. С течение времени их число постоянно возрастает. В глубокой древности наиболее широко применялся преимущественно один вид материала – камень, из которого изготавливались топоры, наконечники для стрел. В камне выдалбливались пещеры для жилья. Следующий важный шаг был сделан несколько тысячелетий назад, когда удалось из оксида железа получить металлическое железо. Появились металлические изделия в виде оружия, предметов быта, несложных приспособлений для обработки земли. И вот заканчивается второе тысячелетие от рождества Христова. Железо как материал по объему производства начинает уступать другим материалам полимерам. С 1980 г., например, в США их производят больше, чем железа. Разнообразная одежда из полиэфира, полиэтиленовая посуда, ковры из полипропилена, мебель из полистирола, шины из полиизопрена и т. п.– все это примеры чрезвычайно большого многообразия применений полимеров.
Многие конструкционные элементы современных самолетов изготовлены из композиционных полимерных материалов. Один из таких материалов – кевлар – по важному показателю – отношению прочность/масса – превосходит многие материалы, в том числе и самую высококачественную сталь.
В последние десятилетия активно обсуждается вопрос об изготовлении автомобиля полностью из полимерных материалов, которые помогут уменьшить его массу и тем самым экономнее расходовать топливо.
К современным материалам относятся и древесина, и стекло, и силикаты, каждый из которых обычно считают традиционным материалом. Древесина служит не только строительным материалом, но и сырьем для производства ценной многообразной продукции. Стекло – материал не новый, но перспективный: в последнем десятилетии изготовлены стекла с удивительными свойствами. Силикатные материалы до сих пор составляют основу строительной индустрии.
Современные пластмассы
Пластмассы – это материалы на основе природных или синтетических полимеров, способные приобретать заданную форму при нагревании под давлением и устойчиво сохранять ее после охлаждения. Помимо полимера, пластмассы могут содержать наполнители, стабилизаторы, пигменты и другие компоненты. Иногда употребляются другие названия пластмасс – пластики, пластические массы.
Пластмассы различаются по эксплуатационным свойствам (например, антифрикционные, атмосферо-, термо- или огнестойкие), виду наполнителя (стеклопластики, графитопласты и др.), а также по типу полимера (аминопласты, белковые пластики и т. п.). В зависимости от характера превращений, происходящих в полимере при формовании изделий, пластмассы подразделяются на термопласты (важнейшие из них создаются на основе полиэтилена, поливинилхлорида, полистирола) и реактопласты (наиболее крупнотоннажный вид из них – фенопласты). Основные методы переработки термопластов –литье под давлением, вакуумформование, пневмоформование и др. Реактопласты формуются прессованием и литьем под давлением.
К настоящему времени налажено массовое промышленное производство различных видов пластмасс.
И пластмассы вполне можно отнести к традиционным материалам, хотя поиск пластмасс с новыми свойствами продолжается.
Прошло более ста лет с момента появления на свет первого органического материала – целлулоида. Сегодня многообразие синтетических веществ настолько велико, что вряд ли возможно их перечислить. Когда идет речь об искусственных материалах, многие имеют в виду прежде всего пластмассы – вещества, созданные в искусственных условиях. В 1980 г. американские ученые впервые обнаружили природную полиэфирную пластмассу в гнездах пчел, живущих в земле.
Массовое производство пластмасс началось во второй половине нашего века. В 1900г. мировое производство пластмасс составило около 20 тыс. т, а в 1970 г. – уже 38 млн. т. Предполагается, что к концу тысячелетия объем производства пластмасс достигнет уровня выпуска стали и составит сотни млн. т в год.
Часто к одному и тому же материалу предъявляются взаимоисключающие требования. Например, материал для зимней одежды должен обладать хорошим теплоизолирующим свойством и эластичностью, но в то же время быть прочным. Строителей интересуют материалы с хорошими тепло- и звукоизоляционными, прочностными и другими свойствами. Всем перечисленным требованиям среди множества материалов в наибольшей степени удовлетворяют искусственные органические соединения – полимеры.
Полимеры построены из макромолекул, состоящих из многочисленных малых основных молекул – мономеров. Процесс их образования зависит от многих факторов, вариации и комбинации которых позволяют получить огромное множество разновидностей полимерной продукции с различными свойствами. Основные процессы образования макромолекул – полимеризация и поликонденсация.
Около 2/3 всего мирового производства полимеров составляют материалы массового промышленного потребления: полиэтилен, политетрафторэтилен, поливинилхлорид, полипропилен и др. Области применения данных полимеров весьма разнообразны – от текстильной промышленности до микроэлектроники. Стоимость их сравнительно невысокая. К остальной части полимерных материалов, составляющей 1/3, относятся полиэфирные смолы, полиуретан, аминопласты, фенопласты, поликрилаты, полиформальдегид, поликарбонаты, фторополимеры, силиконы, полиамиды, эпоксидные смолы и другие виды полимеров.
Изменяя структуру молекул и их разнообразные комбинации, можно синтезировать пластмассы с заданными свойствами. Примером может служить АБС-полимер. В его состав входят три основных мономера: акрилонитрил (А), бутадиен (Б) и стирол (С). Первый из них обеспечивает химическую устойчивость, второй – сопротивление удару и третий – твердость и легкость термопластической обработки. Основное назначение данных полимеров – замена металлов в различных конструкциях.
Термопласты обратимо твердеют и размягчаются, поэтому из них легко формуются изделия разной конфигурации. Искусственные органические вещества, которые не размягчаются при нагревании, называются термореактивными пластмассами или реактопластами. Это фенольные, карбомидные и полиэфирные смолы. Чаще всего в исходном состоянии они представляют собой жидкости, которые при добавлении катализатора или нагревании необратимо затвердевают.
Наиболее перспективными материалами с высокой термостойкостью оказались ароматические и гетероароматические структуры с прочным бензольным кольцом: полифениленсульфид, ароматические полиамиды, фторполимеры и др. Данные материалы можно эксплуатировать при температуре 200–400° С. Раньше такими термостойкими свойствами обладали только неорганические вещества. Разработанные специально для сверхзвуковых самолетов полиимидные пластмассы могут выдерживать температуру до 465° С в течение 30 мин. Главные потребители термостойких пластмасс – авиационная и ракетная техника. Такие пластмассы также находят применение и в автомобиле- и станкостроении, в электротехнике (например, для изоляции проволоки в электродвигателях) и т. п.
С каждым днем растет доля полимерных материалов в строительной индустрии. Пластмассовые рамы, облицовочные материалы, кровля, теплоизоляционные и другие искусственные материалы применяются все чаще в современном строительстве.
Все большую долю материалов составляют разнообразные виды пластмасс для изготовления деталей автомобиля, первенец которого – самодвижущаяся повозка – появился в 1886 г. на улицах Маннгеймера.
За более чем столетнюю историю развития автомобилестроения применялось множество материалов, производимых химической промышленностью, среди которых пластмассы постепенно вытесняли и продолжают вытеснять металл. Так, в 1965 г. на один легковой автомобиль приходилось в среднем 15 кг пластмасс, в 1970 – 25–45 кг. Предполагается, что в ближайшем десятилетии на изготовление одного легкового автомобиля потребуются сотни килограммов пластмассовых материалов, среди которых будут преобладать полиэтилен, поливинилхлорид, АБС-полимеры, полипропилен и др.
Уже производятся легковые автомобили с полностью пластмассовым кузовом. Изготовить весь автомобиль и особенно его двигатель из пластмасс пока не удается. Тем не менее в 1980г. американская фирма демонстрировала автомобильный двигатель из термостойкого пластика, в котором лишь коленчатый вал и поршневые кольца выполнены из металла. Масса данного двигателя оказалась в 2 раза меньше, чем металлического, и потреблял он горючего примерно на 15% меньше, чем обычный. Изготавливаются, кроме того, автомобили с ведущим валом и рессорами из полимерных материалов. В последнее время ведутся работы по массовому внедрению керамических двигателей.
Эластомеры
К полимерным материалам относится и каучук. Многочисленные изделия из данного материала, в том числе и широко распространенная резина, обладают отличительным свойством – эластичностью. Такое свойство объединяет многие эластичные материалы в одну группу эластомеров. Долгое время был известен только один эластичный материал – природный каучук. Он еще и до сих пор добывается из каучукового дерева – бразильской гевеи – таким же способом, как и смола в хвойных лесах, т. е. путем подсечки.
Химия завладела каучуком еще в первой половине XIX в. – в 1841 г., когда американский изобретатель Гудьир предложил способ вулканизации. Хрупкий при низкой температуре и липкий при нагревании сырой каучук при вулканизации переходит в эластичное состояние. При этом его макромолекулярные цепи образуют сетчатую структуру, соединяясь мостиками из атомов серы.
Статистика мирового производства каучука начинается с 1850 г., когда его было добыто около 1500 т. В 1900 г. бразильские леса давали уже 53 900 т каучука. В том же году появился каучук из деревьев, выращенных на плантациях. В последние годы большая часть натурального каучука добывается на крупных плантациях Индокитая. В 1970 г. потребление каучука в мире составило 7,8 млн. т, доля натурального каучука в котором составила около 38%.
Натуральный каучук имеет сравнительно невысокую термостойкость, не отличается высокой маслостойкостью и подвержен старению. Современные методы синтеза позволяют получить синтетический каучук с заданными свойствами. К настоящему времени разработано более 10 видов синтетических каучуков и не менее 500 их различных модификаций. Превосходным качеством отличается силиконовый каучук. Он менее эластичен, чем натуральный каучук, но его свойства в интервале температур от -55 до 180° С очень мало зависят от температуры, и к тому же он физиологически безвреден. Гомогенные и ячеистые полиуретановые эластомеры проявляют отличную износостойкость, высокую химическую стойкость и не подвергаются быстрому старению.
Сфера применения эластомеров весьма разнообразная – от машиностроения до обувной промышленности, но все же значительная их доля идет на изготовление шин, потребность в которых с ростом потока автомобилей постоянно возрастает.
Производя синтетические каучуки, химическая промышленность восполняет дефицит природного сырья – каучука. Точно так же производство синтетической кожи сохраняет сырье животного происхождения. По своим свойствам и качеству многие разновидности современной синтетической кожи мало чем отличаются от натуральной кожи высшего качества.
Синтетические ткани
Внедрение химических технологий в текстильную промышленность началось сравнительно давно – около 200 лет назад, когда с помощью соды и хлорной извести удалось существенно улучшить процессы стирки и отбеливания. Например, с применением хлорной извести продолжительность отбеливания хлопковой ткани сократилась с трех месяцев (при луговой отбелке) до шести часов. Во второй половине XIX в. широко внедрялись синтетические органические красители тканей. С начала XX в. химические технологии стали ориентироваться на создание новых волокнистых материалов. К настоящему времени многообразные искусственные волокна изготавливаются в основном из четырех видов химических материалов: целлюлозы (вискозы), полиамида, полиакрилонитрила и полиэфиров. Более 50% современных волокон производится из материалов, синтезированных за последние 50–60 лет.
На практике широко применяются химическое облагораживание и отделка тканей. Разработаны технологии химической обработки шерсти для обеспечения устойчивости против моли. Найдены способы, позволяющие уменьшить усадку материала, и придающие ему качества несминаемости. Уделяется большое внимание разработке эффективных способов обработки материалов для обеспечения антистатических, антимикробных, грязеотталкивающих и других важных свойств.
Около 50% основных текстильных изделий способны сгорать при нормальных условиях. Снизить горючесть волокон можно двумя путями; специальной обработкой волокон и созданием новых волокнистых жаростойких полимеров. К наиболее перспективным жаростойким полимерам можно отнести ароматические и гетероароматические соединения, длительное время выдерживающие температуру 250–300° С. Содержащие графит волокнистые материалы не теряют своих качеств даже при 1000–2000° С. Разработанные полиэфирные волокна путем включения атомов титана при сохранении механической прочности и гибкости могут противостоять нагреванию до 1200° С.
Среди всех выпускаемых в 70-е годы материалов доля искусственных тканей для одежды составляла около 50%, для товаров домашнего обихода – примерно 25% и столько же для технических целей. Налажено массовое производство высокопрочных кордовых нитей из полиамидов, полиэфиров и вискозы для шинной промышленности.
Объем производства синтетических материалов для изготовления одежды определяется потребительским спросом, в котором за последние годы наметилась тенденция к снижению. Такая тенденция вполне оправдана, ибо синтетические волокна не обладают всем комплексом свойств, присущих естественным волокнам. И одна из важнейших задач химиков – приблизить по свойствам и качеству искусственные материалы к естественным.
Новое поколение тканей, над которыми сегодня работают специалисты, может перестроить наше представление об одежде и ее функциях. Такие ткани сотканы из волокон, которые их изобретатели называют «интеллигентными». За столь обязывающим определением скрываются материалы, обладающие полезными для человека свойствами. При холоде они греют, при жаре – охлаждают, удаляют пот и отвечают другим нуждам кожи. Уже имеются в продаже легкие ткани, обладающие высокой степенью защиты от солнечных лучей. Есть также ткани, пропускающие ультрафиолетовые лучи.
Американский концерн «Дюпон» первое чисто синтетическое волокно – нейлон – выпустил более 60 лет назад. Затем появились акрил, полиамид, полиэстр и другие волокна, родившиеся в лабораторных ретортах. Однако потребители сравнительно быстро оценили как достоинства, так и недостатки синтетических тканей той поры. Рубашка, не нуждающаяся в утюге, вместе с тем летом не давала дышать телу, а зимой не согревала. Эйфория, поднятая первыми синтетическими изделиями, закончилась в основном мусорным ящиком, а не шкафом для одежды.
Немало времени прошло, прежде чем удалось понять и преодолеть границу между природными и синтетическими волокнами. Теперь химия легко воспроизводит лучшие свойства льна, хлопка, шерсти, а естественные материалы давно уже стали предметом многократной химической обработки, придающей, например, хлопку упругость или делающей льняную ткань не столь мнущейся.
Новшества сегодняшнего дня затронули геометрию волокон. Изготовители текстильного сырья стремятся сделать нити возможно тоньше. Тончайшие синтетические нити ткани хорошо видны на фотографии, сделанной под микроскопом (см. рис. 6.13).

Излюбленный материал сегодняшних модельеров – эластик удобен не только в спортивной одежде, но и в повседневных костюмах. Уже существует ткань, в основе которой размещены мельчайшие стеклянные шарики, отражающие свет; одежда из такой материи – хорошая защита для тех, кто ночью находится на улице, например, для регулировщиков автотранспортного движения.
Одна из разновидностей синтетика – кевлар в пять раз прочнее на разрыв, чем сталь, и используется для изготавления пуленепробиваемых курток.
Весьма оригинальна технология изготовления ткани для одежды космонавта, которая способна уберечь его за пределами атмосферы от леденящего холода космоса и палящей жары Солнца. Секрет такой одежды в миллионах микроскопических капсул, встроенных в ткань или в пенопластмассу (см. рис. 6.14).
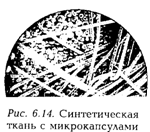
Капсулы содержат парафины. При нагревании они плавятся и отбирают тепло у веществ, находящихся рядом. В конечном счете костюм из подобной ткани становится преградой на пути солнечных лучей к телу человека. Решая обратную задачу – охлаждение, те же парафиновые шарики начинают отвердевать под действием холода, пришедшего снаружи; застывание сопровождается выделением тепла, которое согревает ткань и тело космонавта.
6.11. Традиционные материалы с новыми свойствами
Древесина
Один из видов сырья текстильной промышленности – целлюлоза, вырабатываемая из древесины. Но все же значительная масса древесины идет на изготовление разнообразных пиломатериалов для строительной и мебельной промышленности. Производство целлюлозы для бумажной промышленности составляет 80% и синтетических волокон – 20%.
В мебельной промышленности широко применяются древесностружечные и древесноволокнистые плиты, изготовление которых базируется на органических связующих веществах. Современные химические технологии при производстве древесноволокнистых плит и целлюлозы позволяют использовать любой древесный материал, даже тот, который раньше считался не пригодным для обработки.
Древесина в отличие от ископаемого горючего сырья сравнительно быстро восстанавливается. В этой связи, а также в силу того, что цены на ископаемое органическое сырье будут расти, следует ожидать, что основная доля производства пластмасс, эластомеров и синтетических волокон будет реализована при переработке древесины в промежуточное химическое сырье – этилен, бутадиен и фенол. А это означает, что древесина станет не только строительным материалом и сырьем для производства бумаги, но и важным химическим сырьем для получения искусственных веществ: фурфурола, фенола, текстиля, топлива, сахара, белков, витаминов и других ценных продуктов. Например, из 100 кг древесины можно изготовить примерно 20 л спирта, 22 кг кормовых дрожжей или 12 кг этилена.
Древесина – не единственный вид органического сырья. Другие разновидности биомассы: солома, камыш и т. п. – посредством химических технологий могут превращаться в такие же ценные продукты, что и те, которые производятся из древесины.
Микробиологи обнаружили, что грибы, вызывающие белую гниль древесины, могут приносить пользу. Их способность видоизменять некоторые компоненты древесины положена в основу новой технологии изготовления стройматериалов: после обработки грибом опилки, стружки и другие отходы склеиваются в монолитную массу. Так получают экологически чистые древесные плиты.
Одна из важнейших областей использования древесины – целлюлозно-бумажная промышленность. Мировое производство целлюлозы в середине 70-х годов достигло 100 млн. т в год. В настоящее время из древесины изготавливается основная масса различных видов бумаги и картона. Технология их изготовления сравнительно проста. Вначале кусочки древесины величиной со спичечную коробку превращают в волокнистую древесную массу. Затем после формования и прессования такой массы с добавленными в нее клеем, наполнителями и пигментными красителями осуществляется процесс сушки. Такая относительно несложная технология применяется давно, но все же отличается от той, на основании которой еще в 105 г. пекинский придворный Цай Лунь впервые изготовил бумагу из волокон конопли, льна и тряпок.
Какие же изменения наметились в технологии производства бумаги в последние десятилетия? Изменения прежде всего связаны с появлением заменителя бумаги – синтетического материала. При синтезе природных и искусственных материалов значительно улучшается качество бумаги. Например, введение пластмасс в волокнистую массу повышает прочность, эластичность бумаги, ее устойчивость к деформации и т. д.
Бумага из пластмассы особенно хороша для высококачественного печатания географических карт, репродукций и т. п. Доля производимой пластмассовой бумаги сравнительно невелика.
С развитием электронно-вычислительной техники и массового производства персональных компьютеров бумага перестает быть основным носителем информации. Однако все же возрастание объемов печатной продукции (книг, газет, журналов и т. п.), а также рост производства промышленной продукции, нуждающейся в упаковочных материалах, неизбежно приводит к ежегодному приросту производства бумаги примерно на 5%. А это означает, что потребность в древесине – важнейшем природном сырье – постоянно возрастает.
Стекло
Еще в V тысячелетии до н. э. в древнем Египте выплавлялись первые стеклоподобные материалы. Стеклянная посуда в том виде, как она представляется нам сегодня, изготавливалась в XV в. до н. э. Однако вместе с тем стекло долгое время не находило широкого применения, поскольку ни броню, ни каску, ни даже ручную дубинку из столь хрупкого материала изготовить нельзя.
Первые гипотезы о структуре стекла появились в 20–30-е годы XX в., хотя с древних времен выплавлялись стекла более 800 различных составов, из которых производилось около 43 тыс. разновидностей изделий. Как и прежде, стекло обладает одним существенным недостатком – хрупкостью. Создать стекло нехрупким – одна из труднейших задач даже с учетом современных технологий.
Стекло состоит преимущественно из силикатной массы (до 75% SiO2). Результаты электронно-микроскопических исследований структуры стекла показали, что при охлаждении расплава стекла возникают каплеобразные области, отличающиеся от окружающей их массы расплава химическим составом и стойкостью к химическим воздействиям. Размеры таких областей от 2 до 60 нм. Изменяя величину, число и состав данных областей, можно изготовить стеклянную посуду с очень высокой химической стойкостью. При разделении каплеобразных областей происходит кристаллизация – образуются кристаллы (размером около 1 мкм) со структурой стеклокерамического вещества – ситалла. Таким образом можно изготовить прозрачный или похожий на фарфор материал, коэффициент теплового расширения которого варьируется в таких широких пределах, что его можно прочно соединять с многими металлами. Некоторые стеклокерамические материалы выдерживают высокотемпературный перепад, т.е. не растрескиваются при резком охлаждении от 1000° С до комнатной температуры.
В начале 70-х годов разработана новая разновидность ситалла, который можно обрабатывать, как обычный металл, т. е. его можно обтачивать, фрезеровать, сверлить, а на деталях из него можно даже наносить винтовую резьбу. Область применения ситаллов – автомобилестроение, электротехника, химическое машиностроение, домашнее хозяйство.
Стекло, охлажденное при обычной температуре, имеет прочность на изгиб около 50 Н/мм2, а термически закаленное стекло – примерно 140 Н/мм2. При дополнительной химической обработке получается сверхпрочное стекло с прочностью на изгиб от 700 до 2000 Н/мм2. Химическая обработка заключается в том, что на поверхности стекла небольшие по размеру ионы натрия путем ионного обмена заменяются более крупными ионами калия. Химически упрочненное стекло не разбивается даже при сильном ударе и поддается механической обработке в отличие от термически закаленного стекла.
Высокой прочностью обладают композиционные материалы, включающие химически обработанные стекла со слоями пластика. Такой материал в некоторых конструкциях может заменить металл. Бронестекло толщиной 20–40 мм, состоящее из нескольких склеенных искусственной смолой стекол, не пробивается пулей при выстреле из пистолета.
Иногда для облицовки зданий применяются цветные стекла, та или иная окраска которого достигается введением оксидов металлов. Цветные стекла поглощают инфракрасное излучение. Таким же свойством обладают стекла с напыленным на их поверхность тонким слоем металла или сплава. Данные стекла способствуют поддержанию нормального микроклимата в помещении: летом они задерживают лучи палящего солнца, а зимой сохраняют тепло.
Широко применяются стекловолокнистые материалы. Ими можно армировать, отделывать, склеивать, декорировать, изолировать, фильтровать и т. п. Объем их выпуска огромен – в 1980г. он составлял около 1 млн т/год. Стеклонити для текстильной промышленности имеют диаметр около 7 мкм (из 10 г стекла можно вытянуть нить длинной 160 км). Стеклонить обладает прочностью до 40 Н/мм2, что гораздо прочнее стальной нити. Ткань из стекловолокна не смачивается и устойчива к деформации, на нее можно наносить разноцветные рисунки.
Применение стекловолокна в качестве светопровода породило новую отрасль естествознания – волоконную оптику. Стекловолокна – весьма перспективные средства передачи информации.
Хорошо известны изоляционные свойства стекла. Однако в последнее время все чаще говорят о полупроводниковых стеклах, которые изготавливаются методом тонкопленочной технологии. Такие стекла содержат оксиды металлов, что и обеспечивает им необычные, полупроводниковые свойства.
С помощью низкоплавкой эмали из стекла (570 °С) удалось изготовить надежное покрытие для алюминия. Покрытый эмалью алюминий обладает комплексом ценных свойств: высокой коррозионной стойкостью, эластичностью, ударопрочностью и др. Эмали можно придать различные цвета. Такой материал выдерживает агрессивную промышленную атмосферу, не подвергается старению.
Область применения стеклопродукции постоянно расширяется, а это означает, что уже сегодня стекло становится универсальным материалом. Современное стекло – традиционный материал, обладающий новыми свойствами.
Силикатные и керамические материалы
Постоянно развивающаяся строительная индустрия потребляет все большее количество строительных материалов. Свыше 90% из них – силикатные материалы, среди которых лидирует бетон. Его производство в мире превышает 3 млрд. т/год. На бетон приходится 70% общего объема всех строительных материалов. Самая важная и самая дорогая составляющая бетона – цемент. Его мировое производство с 1950 по 1980гг. увеличилось почти в 7 раз и в 1980 г. достигло почти 1 млрд. т.
Прочность на сжатие обычного бетона составляет 5–60 Н/мм2, а для лабораторных образцов превышает 100 Н/мм2. Высокопрочный бетон получается в результате термической активации цементного сырья при 150° С. Высоким требованиям отвечает полимербетон, но он пока еще дорог. Освоено производство и огнеупорного бетона, выдерживающего температуру до 1800°С. Процесс затвердевания обычного бетона составляет не менее 60–70% общего производственного времени. К сожалению, действенный и легко доступный ускоритель схватывания – хлорид кальция – вызывает коррозию железной арматуры, поэтому производится поиск новых дешевых ускорителей затвердевания. Иногда применяются ингибиторы схватывания бетона.
Находит применение силикатный бетон, состоящий из смеси извести и кварцевого песка, или золы угольных фильтров. Прочность силикатного бетона может достигать от 15 до 350 Н/мм2, т. е. превышать прочность бетона на основе цемента.
Представляет интерес бетон с полимерной структурой. Он легок, в него можно забивать гвозди. Полимерная структура создается введением алюминиевого порошка в качестве расширительной добавки.
Разрабатываются различные сорта легкого бетона из цемента и полимеров небольшой плотности. Такой бетон отличается высокими теплоизоляционными свойствами и прочностью, малым влагопоглащением и легко поддается обработке различными способами.
При введении асбеста в цементный раствор получается асбобетон – широко распространенный строительный материал, весьма стойкий к изменениям погодных условий.
Широкое применение находят керамические материалы. Из керамики производят более 60 тыс. различных изделий – от миниатюрных ферритовых сердечников до гигантских изоляторов для высоковольтных установок. Обычные керамические материалы (фарфор, фаянс, каменная керамика) получают при высокой температуре из смеси каолина (или глины), кварца и полевого шпата. Из керамики изготавливаются крупноформатные блоки, пористый и пустотелый кирпич, а для специальных целей (например, для дымовых труб) – закаленный кирпич.
В последние десятилетия к керамике стали относить и бессиликатные композиционные материалы из различных оксидов, карбидов, силицидов, боридов и нитридов. Такие материалы сочетают в себе высокие термическую и коррозийную стойкость и прочность. Некоторые композиционные материалы начинают разрушаться только при температуре выше 1600° С.
Высокопрочностные материалы, в которых (в результате прессования порошка при 1700° С) до 65% Аl2О3 внедряется в кристаллическую решетку Si3N4 , выдерживают температуру выше 1200° С. В сосудах из такого материала можно плавить медь, алюминий и другие металлы. Из комбинации кремний–алюминий–азот–кислород можно получить многообразные керамические материалы, обладающие высокими техническими качествами.
Металлокерамические композиционные материалы имеют высокую твердость и чрезвычайно высокую термостойкость. Из них изготавливаются камеры сгорания для космических ракет и детали для металлорежущих инструментов. Такие материалы производятся методом порошковой металлургии из металлов (железа, хрома, ванадия, молибдена и др.) и оксидов металлов (преимущественно Аl2О3), карбидов, боридов, нитридов или силицидов. В металлокерамике сочетаются качества керамики и металлов.
Сравнительно недавно – в начале 90-х годов – синтезирован керамический материал на основе оксидов меди, обладающий удивительным свойством – высокотемпературной сверхпроводимостью. Такой материал переходит в сверхпроводящее состояние при 170 К.
Вне всякого сомнения, в результате исследования структуры и свойств новых керамических материалов будут найдены способы синтеза композитов с раньше неизвестными свойствами.
Средства сохранения материалов
Важно не только получить высококачественный материал, но и сохранить его. Воздействие окружающей среды ухудшает качество материала: происходит его преждевременное старение, разрушение и т. п. К существенному разрушению металлов, особенно нецветных, приводит их коррозия, при длительном воздействии влаги древесина подвергается гниению и т. д. Поэтому для сохранения качества материалов и изготовленных из них изделий применяются различные средства защиты.
Принято считать, что человек научился изготавливать металлические изделия более 4500 лет назад, и с тех пор он борется с коррозией. По некоторым оценкам, ежегодные потери железа в результате коррозии составляют почти 15% мировой продукции стали, а это означает, что примерно каждая седьмая домна на земном шаре работает впустую.
Самая распространенная мера защиты от коррозии – окраска, т. е. нанесение защитного слоя масляной или синтетической краски. Слой краски защищает изделия из древесины от гниения. Широко применяются краски на основе алкидных смол.
Обычное покрытие кажется эффективным, когда краска наносится на чистую поверхность. Однако процесс очистки поверхности – трудоемкая операция, поэтому проводится поиск защитных покрытий для нанесения на поврежденную коррозией поверхность без предварительной ее очистки. Одно из таких покрытий уже синтезировано в виде краски, содержащей цианамид цинка, при реагировании которого с ржавчиной образуется цианамид железа, надежно защищающий поверхность от коррозии.
Для приготовления красок и лаков широко применяются органические растворители и разбавители. После нанесения краски органические вещества испаряются, загрязняя атмосферу. Такого недостатка лишены жидкие лаки без растворителей, а также краски, разбавленные водой. Весьма эффективно порошкообразное покрытие электростатическим способом, при котором в качестве связующих веществ применяются термопласты и «сшитые полимеры» (эпоксидные смолы, поливинилацетат, полиолефины). С помощью полиэфиров и высокомолекулярных полиамодов можно получить цветные или прозрачные слои толщиной около 0,02 мм, прочно сцепляемые с окрашиваемой поверхностью.
Представляют практический интерес электропроводящие краски, необходимые для изготовления печатных схем, антенн и т. п.
Антикоррозийными свойствами обладают нержавеющие стали, содержащие дорогостоящие металлы хром или никель. Гораздо дешевле напыление на обычную сталь слоя алюминия или хрома небольшой толщины– менее 0,001 мкм.
Один из перспективных способов защиты от коррозии – формирование слоя своеобразной ржавчины, предохраняющего металл от дальнейшего разрушения. Обычная ржавчина, состоящая из рыхлого слоя оксида железа, способствует дальнейшему разрушению материала. Защитный слой ржавчины образуется на поверхности деталей из стали, содержащей, например, 0,7–0,15% фосфора, 0,25–0,55% меди, 0,5–1,25% хрома и 0,65% никеля. К настоящему времени уже разработаны десятки разновидностей таких сталей, обладающих удивительным свойством самозащиты. Их можно формовать и сваривать, а стоимость их на 10– 30% выше обычных сталей. Из них можно изготавливать вагоны, цистерны, трубопроводы, строительные конструкции и многое другое, что требует устойчивости к атмосферным воздействиям.
Замена материалов
На смену старым материалам приходят новые. Это происходит обычно в двух случаях: когда возникает дефицит старого материала и когда новый материал более эффективен. Материал-заместитель должен обладать лучшими свойствами. Например, к материалам-заменителям можно отнести пластмассы, хотя считать их определенно новыми материалами вряд ли возможно. Пластмассы могут заменить металл, дерево, кожу и другие материалы. Более 1/3 мирового потребления пластмасс приходится на промышленность. Тем не менее, по некоторым оценкам, только 8–15% стали заменяется пластмассами (преимущественно при изготовлении трубопроводов), бетоном и другими материалами. Сталь обладает вполне приемлемым соотношением между стоимостью и прочностью, возможностью варьирования свойств и способов обработки – все эти качества сдерживают быстрое и массовое ее вытеснение пластмассами и другими материалами.
Не менее сложной является проблема замены цветных металлов. Во многих странах идут по пути экономного, рационального их потребления.
Преимущества пластмасс для многих сфер применений вполне очевидны: 1 т пластмасс в машиностроении экономит 5–6 т металлов. На изготовление пластмассовых изделий требуется всего 12–33% рабочего времени, необходимого для изготовления тех же изделий из металла. В производстве, например, пластмассовых винтов, зубчатых колес и др. сокращается число операций обработки и повышается производительность труда на 300–1000%. При обработке металлов материал используется на 70%, а при изготовлении изделий из пластмасс – на 90–95%.
Замена другого широко применяемого материала – древесины – началось еще в первой половине XX в. Прежде всего появилась фанера, а позднее – древесноволокнистые и древесностружечные плиты. В последние десятилетия древесина стала вытесняться алюминием и пластмассами. В качестве примеров можно назвать игрушки, предметы быта, лодки, строительные конструкции и т. п. В то же время наблюдается тенденция увеличения потребительского спроса на товары, изготовленные из древесины.
В дальнейшем пластмассы будут заменяться композиционными материалами, разработке которых уделяется большое внимание.
Сверхпрочные материалы
Ассортимент материалов различного назначения постоянно расширяется. В последние десятилетия создана естественно-научная база для разработки принципиально новых материалов с заданными свойствами. Так, в разработке сверхпрочных материалов достигнуты определенные успехи. Например, сталь, содержащая 18% никеля, 8% кобальта и 3–5% молибдена отличается высокой прочностью – отношение прочности к плотности для нее в несколько раз больше, чем для некоторых алюминиевых и титановых сплавов. Преимущественная область ее применения – авиационная и ракетная техника.
Коррозионностойкий сплав (62–74% кобальта, 20– 30% хрома, 6–8% алюминия) не разрушается в атмосфере кислорода при температуре вплоть до 1050° С, а при более высокой температуре даже серная агрессивная среда не оказывает на него заметного воздействия.
При химико-термической обработке металлических изделий, например, в атмосфере азота, существенно повышаются их прочность и износостойкость. Прочность атомарных связей при такой обработке становится в 100–1000 раз выше прочности лучших марок стали, а это означает, что химически необработанные сплавы обладают вполне определенным запасом прочности. Продолжается поиск новых высокопрочных алюминиевых сплавов. Плотность их сравнительно невелика и применяются они при относительно невысоких температурах – примерно до 320° С. Для высокотемпературных условий подходят титановые сплавы, обладающие высокой коррозионной стойкостью.
Идет дальнейшее развитие порошковой металлургии. Прессование металлических и других порошков – один из перспективных способов повышения прочности и улучшения других свойств прессуемых материалов.
В последние десятилетия большое внимание уделяется разработке композиционных материалов (композитов), т. е. материалов, состоящих из компонентов с различными свойствами. В таких материалах содержится основа, в которой распределены усиливающие элементы: волокна, частицы и т. п. Композиты могут включать стекло, металл, дерево, искусственные вещества, в том числе и пластмассы. Большое число возможных комбинаций компонентов позволяет получить разнообразные композиционные материалы.
Идея изготовления композитов известна давно. Еще в 600 г. до н. э. в Вавилоне была построена башня высотой 90 м из глиняных блоков, в которые была вмешана козья шерсть. Подобная идея заложена в основу получения современных бетона, древесных длит и других материалов. При оптимальном комбинировании веществ с разными свойствами существенно повышается прочность композиционного материала.
Целенаправленное исследование свойств композиционных материалов началось в 60-е годы XX в., когда новые неорганические волокнистые материалы из бора, карбида кремния, графита, оксида алюминия и т.п. начали сочетать с органическими или металлическими веществами. Некоторые волокнистые материалы имеют структуру нитевидных кристаллов, одна из разновидностей которых показана на рис. 6.15. Композиционные материалы с волокнистой структурой обладают удивительной прочностью. Например, канат из борсодержащих волокон толщиной 3 см может выдержать полностью нагруженный четырехмоторный реактивный самолет. Графитовые волокна при 1500° С прочнее стальных при комнатной температуре. Волокнистые материалы из бора, графита и монокристаллического сапфира (А2О3) используются преимущественно в космической технике.
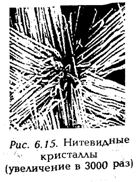
При комбинировании поли- и монокристаллических нитей с полимерными матрицами (полиэфирами, фенольными и эпоксидными смолами) получаются материалы, которые по прочности не уступают стали, но легче ее в 4–5 раз. Благодаря введению металлических матриц из никеля, кобальта, железа, алюминия, хрома и их сплавов повышаются прочность, эластичность и вязкость композитов. Например, алюминий, усиленный боридным волокном, при температуре 500° С имеет такую же прочность, как сталь при комнатной температуре. Композиционный материал из монокристаллических нитей с разнообразными матрицами имеет предел прочности на разрыв более 700 Н/мм2.
Материалом будущего станет такой, который будет не только сверхпрочным, но и стойким при длительном воздействии агрессивной среды.
Материалы, содержащие редкие металлы
Названия «редкие металлы», «редкие элементы», «редкоземельные элементы» не совсем удачны – их содержание в земной коре в среднем сопоставимо или даже выше, чем большинства широко используемых металлов. Например, таких редких металлов, как скандий, церий, лантан, литий, иттрий, ниобий, галлии, в земной коре содержится примерно столько же, сколько хрома, цинка, никеля, меди, свинца. А стронция, циркония, рубидия – гораздо больше.
Полвека назад считали, что редкие элементы не способны концентрироваться в рудах промышленных месторождений. Сейчас известно, что некоторые редкие элементы по концентрации в рудах не уступают и даже превосходят цветные и другие металлы. Редкие металлы находятся в острие пирамиды распространенности химических элементов поверхностного слоя земной коры (рис. 6.16).
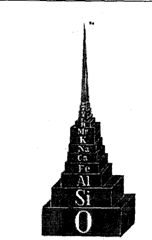
Рис. 6.16. Пирамида распространенности химических элементов в земной коре
Долгое время не находившие широкого применения, сегодня они оказались на острие передовых технологий производства современных многочисленных перспективных материалов. С их применением связаны новые области промышленности, науки и техники – такие как гелиоэнергетика, инфракрасная оптика, оптоэлектроника, лазеры, ЭВМ последних поколений и т.п. Приведем примеры практического применения материалов, содержащих редкие металлы.
Низколегированные стали, в состав которых входит всего 0,03–0,07 % ниобия и 0,01–0,1 % ванадия, позволяют на 30–40 % снизить вес металлических конструкций мостов и многоэтажных зданий, газо- и нефтепроводов, бурильного оборудования и т. п. При этом срок службы конструкций увеличивается в 2–3 раза. Магниты из сверхпроводящих материалов на основе ниобия дали возможность построить в Японии поезда на воздушной подушке, развивающие скорость 577 км/ч.
В легковом американском автомобиле используются примерно 100 кг стали с ниобием, ванадием, 25 деталей из медно-берилловых сплавов, с цирконием и иттрием. При этом вес автомобиля с 1980 по 1990 год уменьшился в 1,4 раза. С 1986г. автомобили начали оснащаться не одним содержащими магнитами. Интенсивно разрабатываются электромобили с литиевыми аккумуляторами, автомобили на водородном топливе с нитридом лантана и др.
Разработаны высокотемпературные топливные элементы на основе оксидов циркония и иттрия, в которых кпд повышается до 65 %. Расход электроэнергии на освещение снижается в 2–3 раза с применением осветительных ламп с люминофорами, содержащими иттрий, европий, тербий, церий.
Арсенид галлия используется в производстве фотоэлементов, интегральных схем и т. п. Применение редкоземельных материалов при крекинге нефти позволяет снизить потребление дорогостоящей платины и увеличить на 15 % выход высокооктанового бензина. Иттрий способен резко увеличить электропроводимость алюминиевого провода и прочность новых керамических конструкционных материалов.
Совсем недавно обнаружилось совсем необычное свойство редких земель – при их внесении в почву повышается на 5–10 % урожаи сельскохозяйственных культур: риса, пшеницы, кукурузы, сахарного тростника, хлопка, фруктов и др.
Чрезвычайно быстро растет потребление редких металлов в станах Западной Европы и Японии. Например, в Японии за период 1960–1985 гг. потребление редких металлов возросло в 10–25 раз.
Результаты исследований показывают, что ископаемое углеводородное сырье содержит промышленно-ценные количества иттрия, лантонидов, ванадия и других редких металлов, цена которых соизмерима со стоимостью самого сырья. Например, в татарской нефти содержится до 700 г/т ванадия, который является ценным, но и весьма токсичным веществом. При извлечении его из нефти решаются задачи: добывается нужный для многих целей металл и предотвращается его рассеяние в атмосфере и на почве.
Некоторые специалисты убеждены: редкие металлы – будущее новой техники. На пороге тысячелетий современная цивилизация переходит из железного века в новый – век легких и надежных материалов, содержащих редкие металлы.
Термостойкие материалы
Новые технологии изготовления той или иной продукции, как правило, базируются на конструкционных материалах, сохраняющих свои свойства за пределами нормальных условий, например, при высокой или сверхвысокой температуре. Высокая эффективность многих аппаратов, двигателей и т.п. достигается при высокой температуре, поэтому создание термостойких материалов – одна из важнейших задач развития современных химических технологий.
К настоящему времени разработаны перспективные способы изготовления термостойких материалов. К ним относятся имплантация ионов на какой-либо поверхности; плазменный синтез – объединение веществ, находящихся в плазменном состоянии; плавление и кристаллизация в отсутствии гравитации; напыление на поликристаллические, аморфные и кристаллические поверхности с помощью молекулярных пучков; химическая конденсация из газовой фазы в тлеющем плазменном разряде и др.
Для изменения локальных химических и физических свойств материалов применяется лазерная технология. Сфокусированный луч мощного импульсного лазера способен кратковременно (в течение 100 нс) создавать чрезвычайно высокую локальную температуру – вплоть до 10 000 К. В точке фокусировки лазерного луча в результате изменения физических и химических свойств происходит локальная модификация поверхностного слоя, в котором может образоваться сплав с заданными свойствами. В условиях конденсации газовой фазы лазерный луч может инициировать химическую реакцию.
С применением современных технологий получены, например, нитрид кремния Si3N4 и силицид вольфрама WSi2 – термостойкие материалы для микроэлектроники. Нитрид кремния обладает превосходными электроизолирующими свойствами даже при небольшой толщине слоя – менее 0,2 мкм. Силицид вольфрама отличается весьма малым электрическим сопротивлением. Из данных материалов напыляются тонкопленочные элементы интегральных схем. Напыление таких термостойких материалов производится методом плазменного осаждения на менее термостойкую подложку без заметного изменения ее свойств.
Представляет практический интерес способ получения новых керамических материалов для изготовления, например, цельнокерамического блока цилиндров двигателя внутреннего сгорания. Данный способ заключается в отливке кремнийсодержащего полимера в форму заданной конфигурации с последующим нагреванием, при котором полимер превращается в термостойкий и прочный карбид или нитрид кремния.
Современные графито-волокнистые материалы, способные выдерживать температуру до 2000° С. Конечно, это не предел. Новые технологии позволяют синтезировать более термостойкие материалы.
Нитинол
Нитинол представляет собой никель-титановый сплав (55%Ti, 45%Ni), обладающий необычным свойством – сохранять первоначальную форму. Поэтому иногда его называют запоминающим металлом или металлом, обладающим памятью. Нитинол способен сохранять свою первоначальную форму даже после холодного формования и термической обработки. Для него характерны сверх- и термоупругость, высокая коррозионная и эрозионная стойкость.
Поначалу нитиноловые изделия служили преимущественно для военных целей – с их помощью в боевых самолетах соединяли различные трубопроводы, доступ к которым ограничен. Соединение производилось муфтой, свободно надевашейся на концы соединяемых трубок. После пропускания электрического тока муфта нагревалась примерно на 30° С и принимала первоначальную форму с меньшим диаметром, плотно прилегая к концам трубок.
Уникальную конструкцию с помощью нитиноловых муфт удалось собрать в космосе. Тогда потребовалось скорректировать орбиту станции «Мир», для чего нужно было на удалении 14 метров от нее расположить двигатель для корректировки орбиты. Монтаж сравнительно длинной мачты для крепления двигателя традиционными методами (с помощью сварки и крепежных материалов) потребовал бы длительного пребывания космонавта в космосе, что могло подвергнуть его чрезмерному космическому облучению. Нитиноловые муфты позволили быстро и легко собрать 14-метровую мачту.
Наибольшую пользу, конечно же, может принести применение нитиноловых муфт не для решения разовых космических и узконаправленных военных задач, а для народнохозяйственных целей. Ведь множество разнообразных трубопроводов проложено по бескрайним просторам нашей планеты. Это газопроводы, нефтепроводы, бензопроводы, водопроводы. Газо-, нефте- и бензопроводы, заполненные легковоспламеняющимися соответственно газом, нефтью и бензином, представляют повышенную пожароопасность, в связи с чем нельзя при их ремонте применять сварку, и все восстановительные работы приходится выполнять с помощью резьбовых соединений и крепежного материала. Данная задача гораздо упрощается с применением коррозионностойких нитиноловых муфт, которые срабатывают при пропускании через них относительно небольшого тока, при этом не требуется открытого огня.
Нитиноловые фиксаторы, муфты, спирали находят применение в медицине. С помощью нитиноловых фиксаторов эффективнее соединяются сломанные части костей. Благодаря памяти формы нитиноловая муфта лучше фиксируется в десне, предохраняя места сочленений от перегрузок. Нитинол, обладая способностью упруго деформироваться на 8–10%, плавно воспринимает нагрузку, подобно живому зубу, и, в результате, меньше травмирует десну. Нитиноловая спираль способна восстановить сечение пораженного той или иной болезнью сосуда в организме человека. При внедрении нитиноловых деталей происходит более эффективное заживление ран – ведь, помимо замечательных механических свойств, нитинол еще и биологически инертен.
Вне всякого сомнения, нитинол – перспективный материал, и в ближайшем будущем станут известны другие примеры успешного его применения.
Жидкие кристаллы
Жидкие кристаллы – это жидкости, обладающие как и кристаллы анизотропией свойств (в частности, оптических), связанной с упорядоченной ориентацией молекул. Благодаря сильной зависимости свойств жидкого кристалла от внешних воздействий они находят разнообразное применение в технике (в температурных датчиках, индикаторных устройствах, модуляторах света и т. п.).
Жидкие кристаллы известны более 100 лет, но практический интерес они вызвали лишь несколько десятилетий назад. Жидкокристаллические индикаторы приборов, калькуляторов, переносных компьютеров – все это стало обыденным и привычным. Сегодня на мировом рынке дисплейных технологий жидкокристаллические устройства уступают разве что кинескопам, а по экономичности потребления энергии в дисплеях с относительно небольшой площадью экрана они не имеют конкурентов.
Жидкокристаллическое вещество состоит их органических молекул с преимущественной упорядоченной ориентацией в одном или двух направлениях. Такое вещество обладает текучестью как жидкость, и кристаллическая упорядоченность молекул подтверждается его оптическими свойствами. Различают три основных типа жидких кристаллов: нематические, смектические и холестирические (см. рис. 6.17).
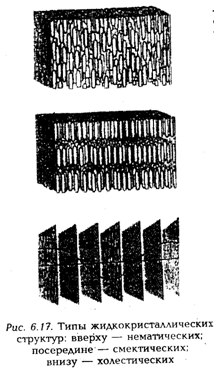
Наименьшую упорядоченность имеют нематические жидкие кристаллы. Молекулы их параллельны, но сдвинуты вдоль своих осей одна относительно другой на произвольные расстояния, т.е. длинные, узкие и в то же время весьма жесткие молекулы выстраиваются подобно сплавляемым по реке бревнам (см. рис. 6.17, вверху). Более сложная форма молекул – в виде плоскостей, из которых образуется многослойная относительно упорядоченная структура, наблюдается в смектических жидких кристаллах (рис. 6.17, посредине). По структуре холестирические жидкие кристаллы похожи на нематические, но отличаются от них дополнительным закручиванием молекул в направлении, перпендикулярном их длинным осям (рис. 6.17, внизу). Шаг такой спиральной структуры может быть очень большим и достигать несколько микрометров.
Под действием даже очень слабого электрического поля может быть нарушено равновесие ориентированных молекул, при этом изменяются оптические свойства жидкокристаллического вещества: например, из прозрачного оно переходит в светонепроницаемое состояние.
Прогресс в создании новых жидкокристаллических материалов во многом зависит от успешного синтеза молекул сферической, стержне- или дискообразной формы. Одно из перспективных направлений в химии жидких кристаллов – реализация данных структур при синтезе полимеров. Молекулярная упорядоченность, характерная для нематических жидких кристаллов, сформированная при полимеризации, сильно влияет на физические, в том числе и оптические свойства синтезируемого вещества. Именно такой принцип лежит в основе производства искусственных волокон с исключительно высоким пределом прочности на растяжение, которые могут заменить материалы для изготовления фюзеляжей самолетов, бронежилетов и т. п.
Блоксополимеры
Молекулы блоксополимеров, составляющих разновидность полимеров, в результате самоорганизации могут принимать форму сферы, чередующихся слоев, стержней и т. п., образуя своеобразный орнамент. Например, трехблочный сополимер формируется из двух полимеров А и В, причем полимер В расположен между сегментами полимера А. В сформированной структуре А–В–А центральная часть обладает свойствами полимера В, а периферийная – полимера А. Если химическая связь между молекулами А и В приводит к отталкиванию, то образуется сферическая структура, в которой молекулы полимера А относительно равномерно распределены в матрице из молекул полимера В.
Расположение молекул в блоксополимере сильно влияет на его механические свойства. Например, блок сополимер, содержащий 1400 молекул бутадиена (В) и 250 молекул стирола (А) и образующий структуру А–В–А, характеризуется достаточно высоким пределом прочности на растяжение. Тот же трехблочный сополимер, но с обращенной структурой, т. е. В–А–В, представляет собой сиропообразную жидкость с близкой к нулю пределом прочности.
При нагревании блоксополимера со структурой А– В–А можно придать ему любую форму, а при охлаждении до комнатной температуре он становится похожим на вулканизированную резину, но в отличие от резины его снова можно нагреть и придать ему другую форму. Такое свойство термопластичности блоксополимеров имеет важное практическое значение.
Оптические материалы
Подобно тому, как в микроэлектронике транзисторы вытеснили электронные лампы, тончайшие кварцевые нити вытесняют медную проволку, из которой в течение длительного времени изготовлялись многожильные кабели. На смену электрическому сигналу, посылаемому по медному проводу, постепенно приходит значительно более информативный световой сигнал, распространяющийся по светопроводящим волокнам.
Прогресс в развитии световолоконной индустрии во многом определился технологической возможностью изготовления высокопрочной кварцевой нити путем химической конденсации паровой фазы. Технология изготовления кварцевой нити относительно проста. Вначале, вещество, содержащее кремний, сжигается в потоке кислорода. В результате образуется фаза чистого диоксида кремния, которая осаждается на внутренней поверхности стеклянной трубки. Затем стеклянная трубка с нанесенным слоем диоксида кремния размягчается и вытягивается в тонкую нить. Толщина полученной таким образом кварцевой нити со стеклянным покрытием составляет примерно 0,1 толщины человеческого волоса.
Совершенствование технологии изготовления кварцевых нитей позволило менее чем за десятилетний срок примерно в 100 раз сократить потери светового потока. Из новых оптических материалов, например, таких как фторидные стекла, можно получить еще более прозрачные волокна. В отличие от обычных стекол, состоящих из смеси оксидов металлов, фторидные стекла – это смесь фторидов металлов.
Волоконная оптика открывает чрезвычайно большие возможности для передачи большого объема информации на большие расстояния. Уже сегодня многие телефонные станции, телевидение и т. п. с успехом пользуются волоконно-оптической связью.
Современная химическая технология сыграла важную роль не только в разработке новых оптических материалов – оптических волокон, но и в создании материалов для оптических устройств для переключения, усиления и хранения оптических сигналов. Оптические устройства оперируют в новых временных масштабах обработки световых сигналов. Например, оптический переключатель срабатывает за одну миллионную миллионной доли секунды (пикосекунду). В современных оптических устройствах используются ниобат лития и арсенид галлия-алюминия. Экспериментальные исследования показывают, что органические стереоизомеры, жидкие кристаллы и полиацетилены обладают лучшими оптическими свойствами, чем ниобат лития, и являются весьма перспективными материалами для новых оптических устройств.
Материалы с электрическими свойствами
В 50-х годах XX в. по мере изучения природы проводимости полупроводников создавались полупроводниковые материалы для электронных устройств. Вначале такими материалами служили преимущественно монокристаллы кремния и германия (см. рис. 6.18) с содержанием в них относительно небольшой концентрации примесей. Полупроводниковыми свойствами, как выяснилось позже, обладают и бинарные соединения, например, соединения галлия и мышьяка, антимонид индия. Из антимонида индия до сих пор изготавливаются высокочувствительные полупроводниковые детекторы для ближней инфракрасной области.
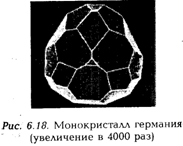
Через некоторое время в центре внимания разработчиков оказались монокристаллы арсенида галлия, выращенные на подложках из монокристаллического фосфида индия. Современная технология позволяет получить несколько слоев арсенида галлия различной толщины с различным содержанием примесей. Из арсенид-галлиевых материалов изготавливают рабочие узлы лазеров и лазерных дисплейных устройств, применяемых в длинноволновых оптических линиях связи.
В процессе разработки новых полупроводниковых материалов были неожиданно открыты полупроводниковые свойства аморфного (некристаллического!) кремния. К настоящему времени открыты совершенно новые группы материалов, обладающих электрической проводимостью. Физические свойства их в значительной степени зависят от локальной структуры и молекулярных связей. Некоторые из таких материалов относятся к неорганическим, другие – к органическим соединениям.
Изучение органических материалов с электропроводящими свойствами началось в конце 60-х, когда были синтезированы проводящие органические кристаллы. Такие проводники были получены в реакциях соединений тетратиафульвалена и тетрационохинодиметана. Молекулы данных соединений имеют плоскую структуру, и в смешанном кристалле они располагаются последовательно, образуя столбы. В результате взаимодействия смежных молекул формируются комплексы с переносом заряда. Такое взаимодействие возможно при наличии донора – молекулы, легко отдающей электроны, и акцептора – молекулы, принимающей их. Роль донора выполняет молекула тетратиафульвалена, а роль акцептора – молекула тетрацианохинодиметана. При переносе заряда между молекулами возникает электрический ток вдоль проводящего столбика.
Механизм переноса заряда в проводящих столбиках обнаружен и в других материалах – полимерных проводниках. В таких проводниках большие плоские молекулы служат элементами проводящего столбика и образую металломакроциклы, соединяющиеся друг с другом посредством ковалентно связанных атомов кислорода. Такая химическая сконструированная молекула обладает электрической проводимостью, и это – настоящая сенсация. Атомы металла и окружающие его в плоском макроцикле группы можно заменить и модифицировать различными способами. В результате можно получить полимер с заданными электропроводящими свойствами.
В углеродном скелете одного из простейших органических полимеров двойные связи чередуются с одинарными. Такая связь называется сопряженной. Она обусловливает подвижность электрических зарядов вдоль углеродной цепи. Данные полимеры с присадками брома, йода и пентафторида мышьяка приобретают металлический блеск и свойство проводить электрический ток лучше многих металлов, например таких, как медь.
Технология изготовления полимерных проводников уже освоена, и число разновидностей таких проводников становится все больше. Под воздействием определенных реагентов полипарафенилен, парафениленсульфид, полипиррол и другие полимеры приобретают электропроводящие свойства.
В настоящее время разрабатываются технологии синтеза полимерных проводников, обладающих прочностью, термопластичностью и эластичностью. Проводятся работы по созданию электрохимическим методом дешевых фотоэлектрических элементов для преобразования солнечной энергии в электрическую. Возможно, с помощью полимерных электродов удастся создать легкие батареи с подзарядкой и большой плотностью аккумулирующей энергии.
В некоторых твердых материалах с ионной подвижной структурой подвижность ионов сравнивается с подвижностью ионов в жидкости. Подобные материалы – твердотельные ионные проводники – используются в устройствах памяти, дисплеях, датчиках, а также в качестве электролитов и электродов в батареях. Например, бета-алюминий натрия служит твердым проводящим электролитом в натриево-серной батарее.
Обычно ионное твердотельное вещество, например хлорид натрия, имеет определенный химический состав и является диэлектриком. При получении твердотельных электролитов создаются структурные дефекты и формируется состав с отличным от целочисленного соотношения между его компонентами. Носители заряда вводятся между слабо связанными слоями решетки, где они могут свободно перемещаться. Такими подвижными носителями заряда могут служить ионы лития или водорода, а матрицу для их внедрения может образовать, например, графит. Ионные проводники на основе диоксида циркония находят применение, например, при изготовлении чувствительных элементов кислородного анализатора выхлопных газов автомобиля.
При создании современной микроэлектронной техники и высокочувствительной аппаратуры используются разнообразные анизотропные материалы с анизотропными электрическими, магнитными и оптическими свойствами. Такими свойствами обладают ионные кристаллы, органические молекулярные кристаллы, полупроводниковые и многие другие материалы. Например, поливинилденхлорид (CH2CCI2,)n, изменяющий форму в электрическом поле, применяется в гидролокаторах и микрофонах. Анизотропные тонкопленочные магнитные материалы служат основой для создания современных высокоплотных накопителей информации.
Современная технология позволяет получить проводящие стекла – материал в виде стекла, но не с диэлектрическими свойствами, а с металлической проводимостью или полупроводниковыми свойствами. Такая технология основана на быстром замораживании жидкости, конденсации газовой фазы на очень холодную поверхность или имплантации ионов на поверхность твердого вещества. Например, некристаллический кремний с полупроводниковыми свойствами можно получить в результате быстрой конденсации продуктов, образующихся в тлеющимся разряде в атмосфере газообразного силана SiH4 . Из данного материала можно изготавливать дешевые солнечные батареи. Рабочие параметры таких батарей в значительной степени зависят от концентрации примесей водорода, химически связанного с неупорядоченно расположенными атомами кремния.
Таким образом, с применением современных технологий можно получить новые материалы с необычным комплексом свойств, не наблюдаемых в традиционных материалах.
Материалы диссоциации металлоорганических соединений
Результаты экспериментальных исследований последнего времени показали, что при термической диссоциации ряда металлоорганических соединений получаются чистые металлы различной твердой формы, обладающие уникальными свойствами. К таким металлоорганическим соединениям относятся:
• карбонилы: W(CO)6, Mo(CO)6, Fe(CO)5 , Ni(CO)4;
• ацетилацетонаты металлов: Сu(С5Н702)2, Pd(C5H702 )2, Pt (C5Н7О2)2 , Ru(C5H7O2)3 ;
• дикарбонилацетонат родия: Rh(C5H7O2)2(СО)2 и др.
Данным соединениям в газообразном состоянии присуща высокая летучесть, они разлагаются при нагревании до 100–150°С. В результате термической диссоциации можно получить чистую металлическую фазу в различных конденсированных формах: высокодисперсные порошки, металлические вискерсы, беспористые тонкопленочные материалы, ячеистые металлоны, металлические волокна и бумага.
Высокодисперсные порошки состоят из частиц малых размеров – до 1–3 мкм. Такие порошки используются для производства металлокерамики – композиций металлов с оксидами, нитридами, боридами, получаемых методом порошковой металлургии. Металлические порошки, например железа и никеля, обладающие магнитными свойствами находят применение в радиоэлектронике и электротехнике.
Металлические вискерсы представляют собой нитевидные кристаллы диаметром 0,5–2,0 мкм и длиной 5–50 мкм. Для таких кристаллов характерны: высокая механическая прочность, примерно в 10 раз превышающая прочность самых высококачественных сталей, высокая устойчивость к окислению, необычные магнитные свойства. Формируются данные кристаллы на активных центрах подложки, где в парамагнитных кластерах образуется своеобразная ступенчатая монокристаллическая структура. Металлические вискерсы представляют практический интерес для синтеза новых композиционных материалов с металлической или пластмассовой матрицей.
Беспористые тонкопленочные материалы отличаются высокой плотностью упаковки атомов. По величине отражения света данный материал приближается к серебру. Беспористое тонкопленочное покрытие толщиной около 90 мкм надежно защищает от коррозии даже в самой агрессивной среде – газовом потоке фтора. Коррозионная стойкость таких покрытий примерно в 5 раз выше, чем покрытий, полученных гальваноосаждением или методом восстановления.
Ячеистые металлы образуются при осаждении металла в результате проникновения паров металло-органических соединений в поры любого материала. Таким способом формируется ячеистая металлическая структура.
Металлизированные волокна и бумага обладают уникальными механическими, теплофизическими и электропроводящими свойствами. В будущем они найдут широкое применение.
Таким образом, современные химические технологии позволяют получить новые материалы с весьма необычными свойствами, некоторые из них уже нашли практическое применение.
Тонкопленочные материалы для накопителей информации
Любая электронно-вычислительная машина, в том числе и персональный компьютер содержит накопитель информации – запоминающее устройство, способное накапливать и хранить большой объем информации. Большинство накопителей информации базируются на магнитной записи. В накопителях информации на подвижном магнитном носителе, где основное – это накопление информации, важным параметром является поверхностная информационная плотность записи, определяемая количеством информации, приходящейся на единицу площади поверхности рабочего слоя носителя информации.
Изготовление современных магнитных накопителей большой емкости основано на применении тонкопленочных материалов. Благодаря применению новых магнитных материалов и в результате совершенствования технологии изготовления всех тонкопленочных элементов магнитного накопителя за относительно короткий срок поверхностная плотность записи информации увеличилась в пять раз: в 1989 г. она составляла примерно 1,55 Мбит/мм2, в 1996г. – 4,65 Мбит/мм2.
Запись с высокой поверхностной плотности осуществляется на носитель, рабочий слой которого формируется из тонкопленочного кобальтсодержащего материала, например, сплава CoPtCr с уникальной магнитной структурой.
Высокую плотность записи можно реализовать только с помощью преобразователей, тонкопленочный материал магнитопровода которых характеризуется большой магнитной индукцией насыщения и высокой магнитной проницаемостью. Такими свойствами обладают пермаллоевые (железоникелевые) пленки, тонкопленочные материалы Fe16N2 с относительно небольшим содержанием азота, многослойные пленки FeSi/NiFe и другие материалы.
Для воспроизведения записанной с высокой плотностью информации применяется высокочувствительный тонкопленочный элемент, электрическое сопротивление которого изменяется в магнитном поле. Такой элемент называется магниторезистивным. Он напыляется из высокопроницаемого магнитного материала, например пермаллоя. Относительное изменение электрического сопротивления пермаллоевого элемента в магнитном поле составляет около 2%. Данная величина, как показали результаты экспериментальных исследований последнего десятилетия, может достигать (например, в многослойных тонкопленочных материалах, однослойных гранулированных пленках и других материалах) десятков процентов, поэтому их называют материалами со сверхгигантским магнетосопротивлением.
Таким образом, с применением тонкопленочных магнитных материалов при изготовлении накопителей информации большой емкости уже реализована довольно высокая плотность записи информации. При модернизации таких накопителей и внедрении новых материалов следует ожидать дальнейшего увеличения информационной плотности, что весьма важно для развития современных технических средств записи, накопления и хранения информации.
Контрольные вопросы
1. Что такое химический элемент?
2. Сформулируйте закон кратных соотношений.
3. Каковы темпы роста химической продукции?
4. В чем заключается специфика современных средств управления химическими процессами?
5. Что такое селективный синтез?
6. Каков молекулярный механизм фотосинтеза?
7. Охарактеризуйте основные виды катализа.
8. Каким образом изучается химический состав космических объектов?
9. Какое процентное содержание химических элементов в верхнем слое земной коры?
10. Охарактеризуйте природные запасы металлов.
11. Назовите основные виды неметаллического сырья.
12. Каковы запасы органического сырья?
13. Как получаются сверхпрочные трансурановые элементы?
14. Что такое остров стабильности?
15. Где применяются радиоактивные изотопы?
16. В чем заключаются преимущества плазмохимической технологии?
17. Почему с повышением давления повышается химическая активность ?
18. Как выращивается искусственный алмаз?
19. Каковы перспективы применения фуллеронов?
20. Как можно изменить свойства синтезируемого полимерного материала?
21. В чем заключается отличительное свойство эластомеров?
22. Какими свойствами обладают современные синтетические ткани?
23. Какое химическое сырье производят из древисины?
24. Как обеспечиваются новые свойства традиционных материалов ?
25. Каковы способы защиты материалов?
26. Назовите основные виды перспективных материалов.
27. Как повышается прочность материалов?
28. Где применяются нитеноловые изделия?
29. Какими свойствами обладают материалы диссоциации металлоорганических соединений?
30. Что такое металлические вискерсы?
.
Комментарии (3) Обратно в раздел Наука
|
|